Book
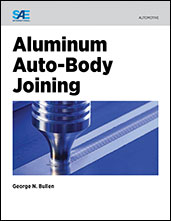
Aluminum Auto-Body Joining
2015-11-11
Fusing aluminum in a multi-material lightweight vehicle is presented via studies on joining dissimilar materials, joining methods, and the performance of the joined materials. The use of aluminum offers a material that embodies properties to meet new standards as the automotive industry continues to pursue improvements in fuel efficiency and emissions. Aluminum’s strength, light weight, and corrosion resistance offers manufacturers a material alternative to steel and an additional material, which has long been known in the industry, to be employed in automotive construction. Topics of technical interest include: • Forming • Galvanic Corrosion • Welding, Fastening, Bonding • Maximizing Weight Benefits Production of strong, lightweight structures will contribute significantly to automobile manufacturers meeting mandated fuel economy standards, as well as customer preferences for utility, comfort, and safety.