Video
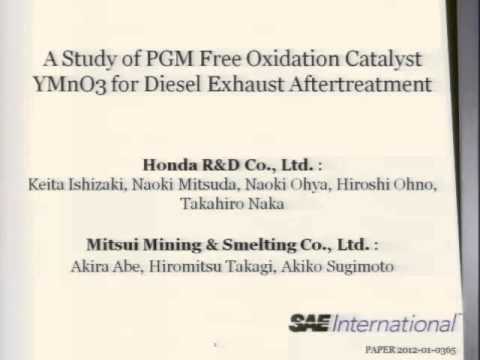
A Study of PGM-Free Oxidation Catalyst YMnO3 for Diesel Exhaust Aftertreatment
2012-06-18
Currently, two consolidated aftertreatment technologies are available for the reduction of NOx emissions from diesel engines: Urea SCR (Selective Catalytic Reduction) systems and LNT (Lean NOx Trap) systems. Urea SCR technology, which has been widely used for many years at stationary sources, is becoming nowadays an attractive alternative also for light-duty diesel applications. However, SCR systems are much more effective in NOx reduction efficiency at high load operating conditions than light load condition, characterized by lower exhaust gas temperatures.