Video
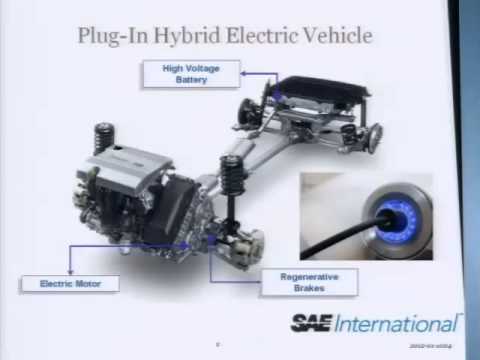
GreenZone Driving for Plug In Hybrid Electric Vehicles
2012-05-29
Impact of driving patterns on fuel economy is significant in hybrid electric vehicles (HEVs). Driving patterns affect propulsion and braking power requirement of vehicles, and they play an essential role in HEV design and control optimization. Driving pattern conscious adaptive strategy can lead to further fuel economy improvement under real-world driving. This paper proposes a real-time driving pattern recognition algorithm for supervisory control under real-world conditions. The proposed algorithm uses reference real-world driving patterns parameterized from a set of representative driving cycles. The reference cycle set consists of five synthetic representative cycles following the real-world driving distance distribution in the US Midwestern region. Then, statistical approaches are used to develop pattern recognition algorithm. Driving patterns are characterized with four parameters evaluated from the driving cycle velocity profiles.