Video
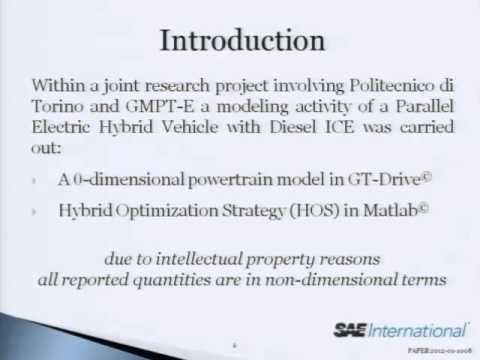
Analysis of Various Operating Strategies for a Parallel-Hybrid Diesel Powertrain with a Belt Alternator Starter
2012-05-30
This paper presents a low-cost path for extending the range of small urban pure electric vehicles by hydraulic hybridization. Energy management strategies are investigated to improve the electric range, component efficiencies, as well as battery usable capacity. As a starting point, a rule-based control strategy is derived by analysis of synergistic effects of lead-acid batteries, high efficient operating region of DC motor and the hydraulic pump/motor. Then, Dynamic Programming (DP) is used as a benchmark to find the optimal control trajectories for DC motor and Hydraulic Pump/Motor. Implementable rules are derived by studying the optimal control trajectories from DP. With new improved rules implemented, simulation results show electric range improvement due to increased battery usable capacity and higher average DC motor operating efficiency. Presenter Xianke Lin